5 min read
Using Far-UVC Technology as a Contamination Control Strategy
Jordi Amagat Molas
:
05 Nov, 2024
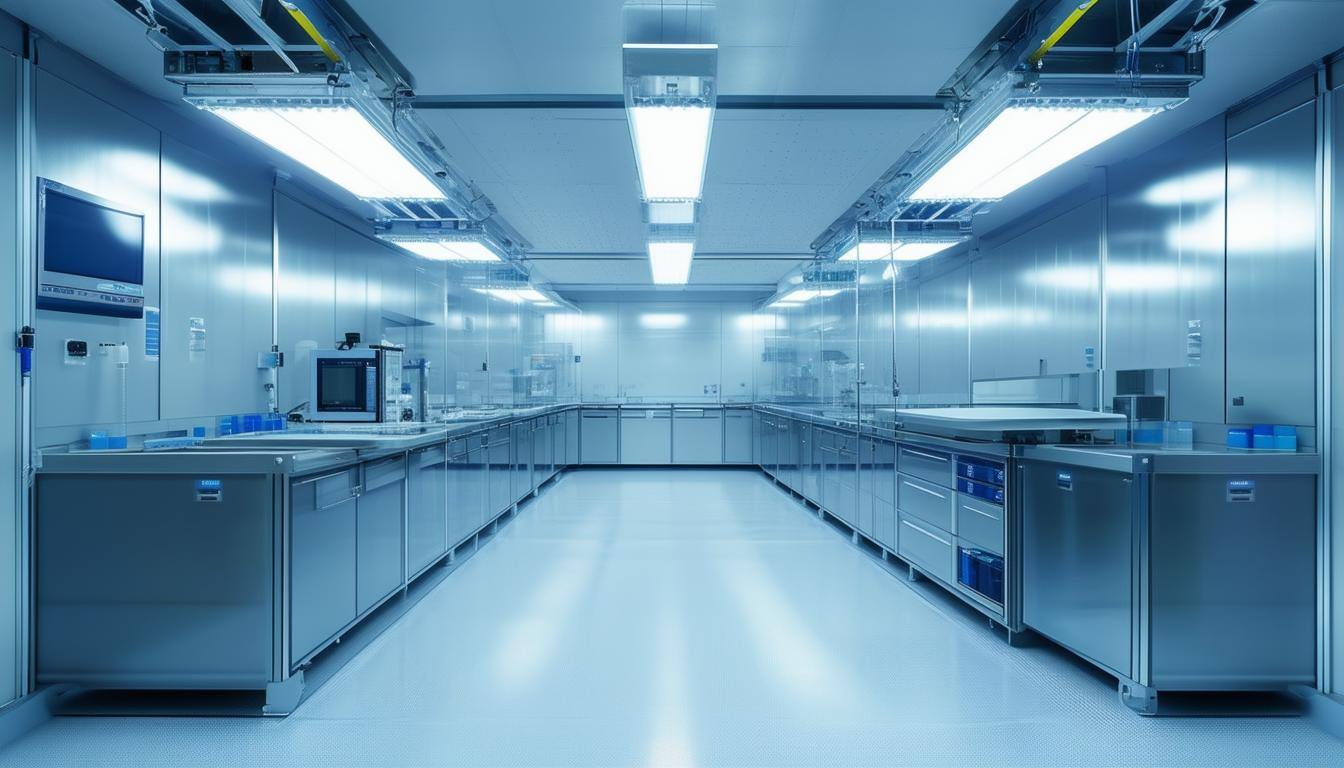
In pharmaceutical manufacturing ensuring sterility is paramount to maintaining product integrity and patient safety. Annex 1 of the EU GMP (Good Manufacturing Practice) guidelines outlines comprehensive requirements for the manufacture of sterile medicinal products. An essential aspect of Annex 1 is the development and implementation of a robust Contamination Control Strategy (CCS).
UV Medico's innovative Far-UVC solutions, the UV222 Booth and UV222 Cleanroom Downlight, are poised to revolutionize contamination control practices by integrating Far-UVC technology into pharmaceutical environments.
Annex 1: Ensuring Excellence in Sterile Manufacturing
Annex 1 specifies the essential requirements for aseptic processing, with an emphasis on minimizing contamination risks through comprehensive control measures:
-
Environmental Monitoring: It mandates stringent environmental monitoring protocols to detect and evaluate microbial and particulate contamination levels in cleanrooms.
-
Personnel Hygiene: The guidelines underscore the critical role of personnel in contamination control, emphasizing appropriate gowning procedures and hygiene practices.
-
Facility Design: Annex 1 prescribes rigorous criteria for cleanroom design and maintenance to achieve and sustain optimal cleanliness levels.
The deadline for compliance with these revised guidelines was August 25, 2023, underscoring the urgency for pharmaceutical manufacturers to adopt advanced disinfection technologies. What is Annex 1?
Contamination Control Strategy (CCS): A Holistic Approach
A Contamination Control Strategy is a structured plan that delineates measures for preventing, detecting, and mitigating contamination risks across the manufacturing process. A robust CCS integrates multiple layers of control, including:
-
Risk Assessment: Identifying potential contamination sources and evaluating the associated risks.
-
Preventive Measures: Implementing proactive measures, such as facility design and environmental controls, to mitigate identified risks.
-
Monitoring and Verification: Establishing rigorous monitoring protocols to ensure the effectiveness of preventive measures.
Strategic Integration of Far-UVC Technologies
Integrating UV Medico’s Far-UVC solutions into your facility’s Contamination Control Strategy offers several key benefits:
-
Enhanced Microbial State of Control: Achieve superior levels of microbial inactivation, thereby reducing the overall contamination risk.
-
Regulatory Compliance: Align with the detailed requirements of Annex 1, ensuring that your facility meets the highest standards for sterile product manufacturing.
-
Operational Efficiency: Benefit from rapid, effective, and safe disinfection methods that do not impede operational workflows.
-
Workforce Safety: Provide a safer working environment by utilizing technologies that are harmless to personnel while effectively targeting harmful pathogens.
UV Medico’s Far-UVC solutions provide an innovative layer of contamination control that aligns seamlessly with these principles.
UV Medico's Far-UVC Solutions: Innovation and Safety
UV222 Booth: Decontaminate Gowned Personnel
The UV222 Booth supports the complexity of the gowning process by reducing the contamination of gowned personnel:
-
Accelerated Decontamination: Utilizing filtered Far-UVC, the UV222 Booth achieves rapid decontamination of gowned personnel in less than 30 seconds, reducing microbial load before entry into critical areas.
-
Broad-Spectrum Efficacy: This technology effectively inactivates a diverse range of microorganisms, including bacteria, viruses, and fungi, thereby significantly reducing environmental deviations and recovery-rates in cleanrooms high-grade areas.
-
User-Friendly Interface: The UV Booth’s touchless operation and intuitive design ensure ease of use while maintaining high safety standards.
-
Regulatory Compliance: By minimizing the microbial burden on personnel, the UV222 Booth supports compliance with Annex 1 requirements for personnel hygiene and contamination control.
UV222 Cleanroom Downlight: Continuous Environmental Decontamination
The UV222 Cleanroom Downlight signifies a transformative change in environmental decontamination:
-
Continuous Decontamination: The Downlight provides ongoing decontamination of air and surfaces, ensuring a consistently decontaminated environment within cleanrooms and critical production areas.
-
Safety in Occupied Spaces: Far-UVC operates at a wavelength of 222 nm, which remains within the outer dead layers of skin and eye, making it safe for use in occupied spaces without posing health risks to staff.
-
Integration and Efficiency: Easily integrated into existing cleanroom infrastructure, the Downlight offers a seamless enhancement to contamination control strategies without disrupting established workflows.
-
Comprehensive Coverage: Its broad-spectrum antimicrobial efficacy ensures the reduction of airborne and surface contaminants, addressing both particulate and microbial contamination risks.
UV Medico’s Far-UVC products, including the UV222 Booth and UV222 Cleanroom Downlight, represent the forefront of contamination control technologies. By incorporating these advanced solutions into your Contamination Control Strategy, pharmaceutical manufacturers can achieve compliance with Annex 1, enhance operational efficiencies, and safeguard both product integrity and personnel health.
For further information and to explore how UV Medico can support your contamination control efforts, feel free to book a meeting with me here.
Sing up our newsletter for more Cleanroom news.
FAQ for Cleanroom Managers
-
What is Far-UVC technology, and how does it enhance contamination control in cleanroom environments?
Far-UVC technology employs ultraviolet light at a wavelength of 222 nanometers to inactivate any type of microorganisms, including bacteria, viruses, and fungi. This technology is particularly advantageous for cleanroom environments as it offers continuous microbial load reduction, aiding in compliance with stringent regulatory standards, such as Annex 1 of the EU GMP. Notably, Far-UVC can be safely used in occupied spaces, such as corridors, airlocks, production rooms, etc, ensuring ongoing decontamination without compromising personnel safety.
-
What Far-UVC solutions does UV Medico provide, and how can they be integrated into existing cleanroom protocols?
UV Medico offers several innovative Far-UVC solutions for cleanroom contamination control: Here are the two main ones:
UV222 Booth: Designed for the rapid decontamination of gowned personnel, reducing microbial load in ony 20 seconds. This solution is essential for minimizing personnel-associated contaminants.
UV222 Cleanroom Downlight: Facilitates continuous air and surface decontamination within cleanrooms, ensuring consistent microbial control without disrupting operational workflows.
These solutions can be seamlessly integrated into existing cleanroom protocols, enhancing overall contamination control strategies and supporting compliance with regulatory requirements.For the rest of our cleanroom products, visit our product page.
-
What specific advantages do the UV222 Booth and UV222 Cleanroom Downlight provide in terms of contamination control and regulatory compliance?
The UV222 Booth offers rapid, highly efficient decontamination of personnel, significantly reducing the risk of contamination upon personnel entry into critical areas. It supports compliance with Annex 1 by ensuring a low microbial load on personnel, reducing environmental deviations and recovery rates, vital for maintaining aseptic production.
The UV222 Cleanroom Downlight ensures continuous and unobtrusive decontamination of both air and surfaces, maintaining a high standard of cleanliness that aligns with stringent regulatory guidelines. This ongoing microbial state of control is essential for mitigating contamination risks and maintaining a controlled environment. -
Is the Far-UVC technology safe for use in occupied cleanroom spaces?
Far-UVC technology is specifically designed to operate at a wavelength centered at 222 nm, which does not penetrate the outer, dead layers of human skin or the outer tear layer of the eye, rendering it safe for use in occupied spaces. This allows for continuous decontamination of the cleanroom environment without posing health risks to personnel, ensuring both operational efficiency and safety.
In addition, Far-UVC technology does not penetrate any type of gowning materials worn by cleanroom operators.
If you would like more details, contact us here.
-
How does the UV222 Cleanroom Downlight enhance the existing decontamination protocols within a cleanroom?
The UV222 Cleanroom Downlight enhances existing decontamination protocols by providing continuous, broad-spectrum antimicrobial efficacy against airborne and surface contaminants.While temporary, cyclic cleaning routines provide high-efficient decontamination, is in between those cycles when contamination occurs. By installing the UV222 Cleanroom Downlight in your cleanroom areas, continuous protection is ensured against unwanted environmental deviations.
Its integration into the cleanroom ceiling design ensures uninterrupted operation, thereby maintaining an aseptic environment with minimal human intervention. This proactive decontamination approach complements traditional cleaning protocols, resulting in optimized contamination control and improved adherence to regulatory standards.
The UV222 Cleanroom Downlight offers multiple software customization options, to ensure continuous contamination control at all times.
We also offer multiple customization options for ceiling suspended fixtures. For more information, please contact us.
-
How do UV Medico’s Far-UVC solutions contribute to a robust Contamination Control Strategy (CCS) in compliance with Annex 1 of the EU GMP?
UV Medico's Far-UVC solutions contribute significantly to a robust Contamination Control Strategy (CCS) by delivering advanced decontamination technologies that align with the comprehensive requirements of Annex 1 of the EU GMP. By integrating the UV222 Booth and UV222 Cleanroom Downlight into cleanroom environments, pharmaceutical manufacturers can achieve superior microbial control, enhance environmental monitoring, and maintain stringent hygiene standards. These solutions not only support regulatory compliance but also optimize operational efficiency, ensuring a safer, more controlled manufacturing environment.