3 min read
3 min read
How to Comply with Annex 1 in Aseptic Filling Lines with UV222 Linear
Emilie Hage Mogensen
:
5/1/24 2:01 PM
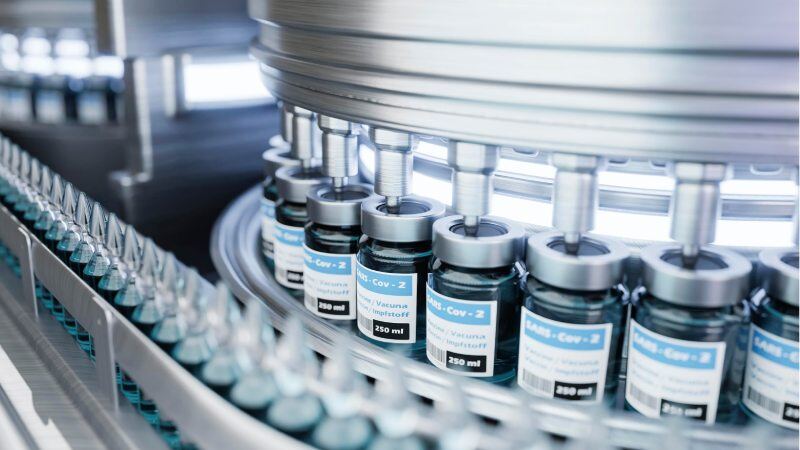
Compliance with Annex 1 of the guidelines regarding the manufactured sterile medicinal products is fundamentally crucial in ensuring the safety and efficacy of pharmaceuticals. This annex, focused on aseptic processing and sterile drug products, emphasizes the importance of maintaining an environment that reduces the risk of contamination. Among the technologies that can aid in achieving compliance, the UV222 Linear lamp stands out as a noteworthy solution, particularly in the context of aseptic filling lines.
Understanding Annex 1 Requirements in Aseptic Filling Lines
The primary aim of Annex 1 is to safeguard the manufacturing process from microbial, particulate, and pyrogen contamination. For aseptic processing environments, this means stringent control over the cleanroom conditions, including air quality, personnel hygiene, materials, and equipment. Specifically, it requires robust microbial control to prevent the introduction, growth, and proliferation of contaminants.
The Aseptic Challenge
The very nature of aseptic filling lines, where products are filled and sealed in a non-sterile environment, mandates superior control strategies to mimic the sterility achieved in terminal sterile products. It's a complex dance of ensuring equipment sterility, cleanroom air quality, and personnel discipline, all while maintaining operational efficiency.
Advancing Sterility Assurance: Innovative Strategies for Contamination Control in Aseptic Processing
In the complex landscape of aseptic processing and stringent cleanroom standards, particularly those governed by Annex 1, the essence of contamination control cannot be overstated. Ensuring the integrity of pharmaceutical products hinges significantly on advanced detection strategies and an unwavering commitment to maintaining a contamination-free environment. Distilling this complexity into manageable insights, we underscore the importance of innovative practices in safeguarding sterility across production operations.
To align with Annex 1 requirements, it is imperative to employ a suite of modern contamination control technologies like the Cleanroom Downlight and UV222 Linear. These tools not only identify potential contamination sources with unparalleled accuracy but also facilitate swift corrective actions. The integration of such technologies into the manufacturing ecosystem represents a cornerstone of proactive risk management, vital for the delivery of safe, effective pharmaceuticals.
In essence, the journey towards full compliance with Annex 1 and beyond is underpinned by a relentless pursuit of excellence in contamination control. By embracing state-of-the-art solutions and fostering a culture of continuous improvement, manufacturers not only meet but exceed the highest standards of product safety and integrity. This commitment not only augments the well-being of end-users but also solidifies a manufacturer's reputation as a stalwart in the domain of cleanroom technology, trusted by professionals across pharmaceuticals, biotech, and healthcare industries.
The UV222 Linear Solution
The UV222 Linear emerges as an ingenious ally in this meticulous process. Designed for deployment in operating theatres, it boasts versatility that makes it equally at home in the stringent environment of aseptic filling lines. Let's delve into how this innovative technology meets, and in some aspects surpasses, the Annex 1 criteria:
1. Continuous Air and Surface Decontamination
The UV222 Linear seamlessly integrates visible light with continuous decontamination of both air and surfaces. Its utility in operating theatres—a benchmark for sterile environments—translates perfectly to aseptic filling lines, offering a dual effect of visible and Far-UVC light at 222 nm. Notably, it can function as a standalone unit or be integrated with Laminar Air Flow (LAF) systems, assuring effective, chemical-free microbial control without risking product or personnel safety.
2. Targeted Microbial Load Reduction
In the heart of the UV222 Linear is its Far-UVC technology operating at 222 nm, which has been proven to significantly reduce microbial load. This is particularly crucial in aseptic filling lines, where the minimization of microbial contamination is key to product safety. Its ability to inactivate viruses, bacteria, and fungi, while being safe for human exposure, aligns with the Annex 1 emphasis on microbial control.
3. Enhanced Cleanliness and Safety Standards
The flexibility and efficacy of the UV222 Linear render it an indispensable asset for upholding the cleanliness and safety standards essential for sterile drug manufacturing. Its integration guarantees not only compliance with Annex 1 requirements but also enhances overall productivity and safety in aseptic filling lines.
4. Improved Visibility and Reduced Fatigue
The illumination system embedded within the UV222 Linear delivers potent white light, ensuring true and distinct colors with a high color rendering index (CRI) and minimal flicker. This feature is vital in reducing the fatigue of operators, thereby indirectly promoting a more attentive and hygienic work environment.
Conclusion
Achieving compliance with Annex 1 in aseptic filling lines is undeniably challenging, yet undeniably crucial for ensuring the safety and integrity of sterile medicinal products. The UV222 Linear offers a technologically advanced and versatile solution that not only meets the stringent requirements laid out in the guidelines but also provides additional benefits that enhance the overall sterility assurance of the manufacturing process. By integrating UV222 Linear into the aseptic filling lines, pharmaceutical manufacturers can significantly bolster their contamination control strategies, ensuring a safer product for the end users and full compliance with regulatory standards.
Latest knowledge from UV Medico
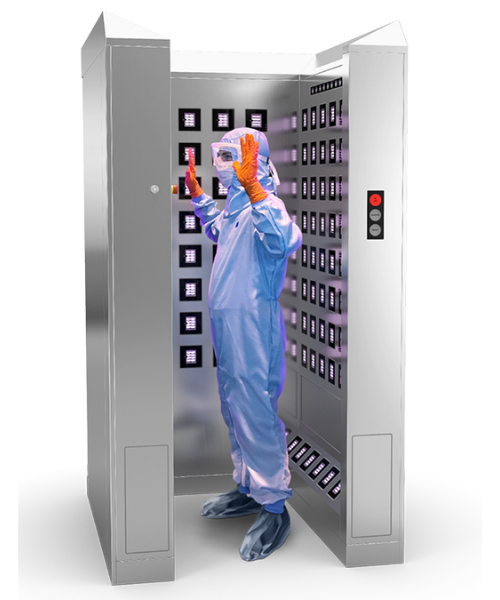
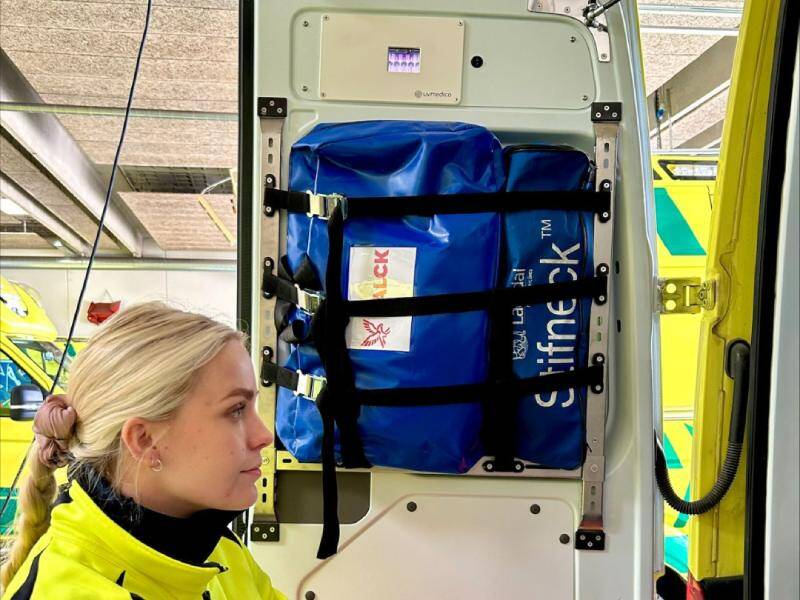
4 min read
UV Medico & Falck: Elevating Ambulance Safety with UV222 Technology
